1、設計情報転写論で捨象されたこと
設計情報転写論を提唱する藤本隆宏教授の経歴をザットみると、こんな感じでしょうか。
大学時代の水の流れの秩序の研究(水利慣行調査)から「産業の進化論」につながり、ものづくりを設計情報の転写で抽象化した「設計情報転写論」を発案する。ハーバード大で自動車製品開発調査(博士論文)後、東大でトヨタ的自動車開発・生産システムの研究を行う。開発・生産の流れを設計情報転写の速度と密度で記述する設計情報転写論をベースに、製品アーキテクチャー論、サイバー空間(上空)―サイバーフィジカルシステム(低空)―物理空間(地上)とする三層構造論で変遷するものづくりの環境変化を捉え、次代のものづくりの在り方を指南する。藤本教授が強調するものづくりのキーワードは「流れ」。その「流れ」を一貫して設計情報転写論で主張している。
ここまで、藤本教授の発信情報をいくつかの切り口でみてきましたが、基盤としている設計情報転写論では生産ラインの基本特性が捨象され、「流れ」の良し悪しを示すリードタイムを記述するアルゴリズムが欠如していることが判明しました。藤本教授はごく最近まで(少なくとも2023年秋ごろまで)、そのことに気が付いていなかったようです。
気になるのが、藤本教授の講義を受講した学生、東大ものづくり経営研究センター(MMRC)の受講者、後継教授陣およびメディアを通じて彼の主張に接した一般の方々への影響です。生産ラインのリードタイムを記述できない設計情報転写論で「流れ」を論じるという愚を四半世紀以上続けてきた影響は決して小さくはないでしょう。
2、現場改善会計論
どんな影響がでているのか、その痕跡を探してみたいと思います。下記の論文があります。J-STAGE はこちら
現場改善会計論の提唱―原価管理から余剰生産能力管理へ―
(日本管理会計学会誌 管理会計学2023 年第31 巻第2 号)
愛知工業大学経営学部教授 柊 紫乃
要旨を引用します。
<論壇要旨>
本稿は日本管理会計学会2022 年度年次全国大会の統一論題テーマ「わが国におけるコスト・マネジメントの現状と課題」をふまえ,企業競争力の源泉のひとつとされる現場改善に注目し,それを支援するコスト・マネジメントについて考察する。京都大学の上總康行名誉教授とともに筆者が提唱する現場改善会計論(Gemba Kaizen Costing, GKC) は、トヨタ生産システムと「設計情報転写論」に依拠する。GKC では,原価計算に「機会損失」概念を導入することで改善効果の会計的測定を可能とした。さらに,コスト・マネジメントの視点を、改善により創り出された余剰生産能力というアウトプット管理へと変化させた。本稿では、GKC の概要のほかに,企業の実践事例を通じて、理論の実務貢献可能性についても検討する。
本論文は“トヨタ生産システムと「設計情報転写論」に依拠”した現場改善会計論です。ここでは、致命的な欠陥を抱えた「設計情報転写論」が本論文の論理の展開や構築にどのような影響を及ぼしたかを中心にみてみようと思います。
現場改善会計論(Gemba Kaizen Costing;以下GKC)の主張、論理構成のポイント等を私なりに次項の
3、先行研究
4、現場改善会計論の論理的枠組み
にまとめてみます。
3、先行研究
改善に寄与するという視点からの先行研究についての評価は次の通り。
標準原価計算
時代の推移とともに標準原価計算の役割が相対的に低下した。標準原価計算のみでは、現場改善を細部にわたり金額測定することは難しい。
活動基準原価計算、活動基準管理他
対象が製造間接費に限られ、個々のアクティビティに含まれるムダの測定がされていない。
マテリアルフローコスト会計
加工費に含まれるムダは考慮されないため、生産現場の加工プロセス改善に対応しきれない。
CAM-I
24時間365日を最大値とする加工時間のみが想定されており、コスト・マネジメントの網羅性という点で限界がある。
スループット会計(制約理論)
企業の財務管理数値との間に計算構造上のつながりが必ずしも担保されていない点に限界がある。
Lean Accounting
リーン思想にもとづいて会計の計算構造も極力簡単にすべきだと主張されたため、コスト・マネジメントとしては単純化しすぎた点に限界がある。
このように、従前のコスト・マネジメント手法には各々に優れた特徴はあるものの、本研究が重視する「改善に寄与する」という視点からみれば限界があるといわざるを得ない。そこで、現場改善とその促進に注目したコスト・マネジメント手法の開発が必要であるという結論にいたった。原価計算の構造と矛盾することなく、かつ、生産現場の改善を支援できる会計理論とその具体的手法について検討を続けており、現時点での成果をGKCとして公表している。
4、現場改善会計論の論理的枠組み
4.1 狙いと依拠
狙い;生産現場での改善効果を見える化し、それを支援する会計理論と具体的手法の開発。
依拠する理論・システム・・・トヨタ生産システム、設計情報転写論。
$ 設計情報転写論に依拠して
「改善とは,現状をより良く改めることである(新郷1954, 23; Shingo 2007, 13)」というシンプルな定義がある。この定義において「何を」より良くするのかを明確にするため設計情報転写論における「ものづくり」の考え方を援用する。藤本教授によれば,「(上流から)設計情報を製品に作り込み(工程ごとに付加価値を転写しながら)、お客様のもと(下流)へ、よどみなく流すことが「ものづくり」であり、よどみをなくす行いがすなわち改善活動である。藤本教授の設計情報転写論を援用することにより,本研究における改善を「現場における(モノや情報の)良い流れを実現すること」と定義した。
改善活動とは、設計情報を製品に作り込み、お客様のもとへよどみなく流れるようにすること、つまり、「(モノや情報の)良い流れの実現」である。
$ トヨタ生産システムに依拠して
大野耐一氏が示された作業の3 分類(作業をしていく上でなんら必要のないもの、付加価値のない作業、正味作業)を援用することで,改善対象とする現場のムダについて「生産現場に投入された経営資源(生産)のうち顧客に届く良品の生産に貢献しなかったものはすべてムダである」と定義した。
改善対象は、現場の「ムダの排除」
4.2 改善効果を「生産能力の増大」で捉え、アウトプット管理へ
生産性とは、「インプット(生産要素の投入)とアウトプット(経済的に有用な産出)の比率」のことである(藤本2001, 117)」。生産性向上とは,インプットされた経営資源(生産)とアウトプットされる良品の比率(正味率)が向上することである。GKCではこれを「生産能力の増大」とよぶ。改善活動による生産能力増大(生産性向上)の効果は次のようになる。
・需要があるとき➡売上増
・需要不足のとき
変動費➡原価低減が実現
固定費➡余剰生産能力=機会損失の発生
需要がない場合、余剰生産能力は「機会損失」となる。「機会損失」という概念を導入することで改善効果の会計的測定を可能とした。さらに、コスト・マネジメントの視点を改善により創り出された余剰生産能力というアウトプット管理へと変化させた。
4.3 改善効果の類型化
図 に示す改善効果の類型化は,生産能力増大の結果として現れる改善の金額的効果についての可能性を網羅する。個々の企業の意思決定によりフローは変わりえるが、この類型図の活用により、現段階での改善効果の見える化が実現するだけでなく、将来の改善効果の想定も可能となる。
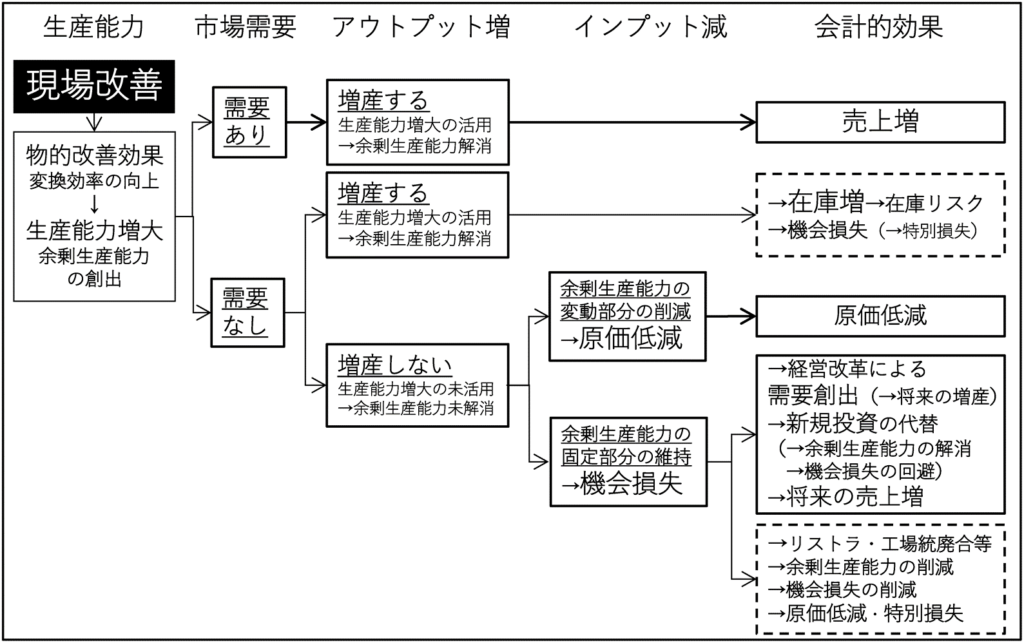
図 現場改善による会計的効果の類型図(現場改善会計論の提唱より)
5、GKCの論理的枠組みの背景を確認する
本論文では、この後、矢橋ホールディングスの事例紹介に移り、具体的なデータでの計算例などが出てきますが、その前に、GKCが設定した論理的枠組みの背景について理解を深め、確認しておきたいと思います。
5.1 トヨタ生産システムと「設計情報転写論」に依拠する背景は
先ず、GKCがトヨタ生産システムと「設計情報転写論」に依拠する背景を探ってみたいと思います。
GKCの狙いは、
狙い;生産現場での改善効果を見える化し、それを支援する会計理論と具体的手法の開発
です。先ず、「改善効果が見える会計理論」を目指すGKCが明確にしたのは改善活動の定義。依拠したものは、トヨタ生産システムと「設計情報転写論」。改善活動とは「ムダの排除」と「(モノや情報の)良い流れの実現」であるとして、「ムダの排除」はトヨタ生産システムに、「(モノや情報の)良い流れの実現」は「設計情報転写論」に依拠する、としています。
「(モノや情報の)良い流れの実現」は「設計情報転写論」に依拠とのことですが、実は、トヨタ生産システムも「流れ」を重視しています。ジャスト・イン・タイムとは「良い流れ」が達成された状態だとみることができます。
だとすれば、GKCは「ムダの排除」も「(モノや情報の)良い流れの実現」もトヨタ生産システムに依拠する、としてもいいのではないでしょうか。なぜ、「設計情報転写論」を持ち出さなければならなかったのでしょうか。
その理由は、経営管理に資する管理会計として、GKC では,「設計情報転写論」における「良い流れ」の対象を、生産現場のモノと情報(生産情報)だけではなく「お金の流れ(柊2019a,2020b)」にも拡張している、からだと思われます。藤本教授は「設計情報転写論」の適用領域を生産現場だけではなく、医療現場、建築現場そしてスーパーなどのサービスの現場に拡張する「広義のものづくり」を提唱しています。管理会計の立場からすれば、製造現場の「モノや情報の流れ」とともに「お金の流れ」も同じ理論体系の中で扱うことができるとなれば、画期的な管理会計論になる、と考えたのではないかと推察されます。
5.2 GKCは過去の会計論に頼らず
生産現場での改善については、関係はあるにしても、管理会計学者からみれば、異分野ではないかと思います。トヨタ生産システムや「設計情報転写論」など、既にあるシステムや理論に依拠することは理解できますが、会計論部分はこれまでの理論に頼ることなく、逆にその不備を指摘します。それらを乗り越える新たな会計理論を目指そうとする強い意力を感じます。
日夜、改善に励む生産現場からみる会計とはどんな風にみえるのか、私の経験談を少々。
工場では毎月、経理資料を基に、原価検討会が開催されていました。標準原価計算システムの基、部門ごとや代表的な製品の原価が発表されます。原価差異の大きい製品や工程、原材料などが指摘されます。担当者はその理由を説明しなければなりません。何でコストが標準より高くなったか、理由がわからないものが大部分。説明に苦労したものです。
現場では、毎日、コスト・ダウン、コスト・ダウン。工数削減効果を金額で評価するのに賃率が使われていました。工数削減時間に賃率と月産数を掛けて月当たりコスト・ダウン額を計算します。社内工程の一部を外注に出すと、社内と外注の賃率差分に数量を掛けてコスト・ダウン額を計算します。右肩上がりの時代はそのようなコスト・ダウン額と工場全体の利益改善はだいたい合っていました。
売れるモノしかつくってはいけない時代になると、利益が出にくくなります。そうなると、さらに賃率の安い中国に出すようになりました。社内の人員が余剰状態になっても中国への外注化の流れは止まりません。中国に出すと輸出入手続き等で3カ月。管理のタイムラグは長くなり、仕掛在庫は急増しました。賃率重視の原価計算信仰の弊害に気が付いたころにはリストラの風が吹いていました。
私の経験からも現場改善という視点から見れば、これまでの原価計算に不都合な部分があることは否めません。現場改善とその促進に注目したコスト・マネジメント手法の開発が必要、ということには全面的に同意します。
5.3 GKCの目標達成はどの程度かー余剰生産能力管理および事例でみる
現場改善を支援できる会計理論とその具体的手法の開発で注目されるのが、モノの流れだけではなく、貨幣価値情報の「流れ」も同じ理論の枠組みで捉えられるようにしようとしていることです。そこで大きな役割を果たすのではないかと考えられるのが、モノだけではなく設計や生産に関する情報、サービス情報、貨幣価値情報などの「良い流れの実現」を目指す「設計情報転写論」です。
ところが、すでに申し上げていますように、「設計情報転写論」には致命的な欠陥があります。それは「流れる時間」を捉えるアルゴリズムがないことです。一般の生産ラインではリードタイムの大部分が待ち行列現象による待ち時間で占められますが、それを捉えることができません。
このような欠陥を抱えた「設計情報転写論」ですが、それをベースにして、GKCでは、どのような方法・手順で、余剰生産能力管理を行うのか、そして矢橋ホールディングスの事例ではどのようなデータ処理を行ったのか、次回、みてみることにします。